LINE BALANCING
Description
Line Balancing is a technique that ensures that the capacity in the process is balanced with the quantity requested from the customer (Takttijd). There should be no shortages or inventory of unsold products.
When
In the Thinking Improvements phase.
Goals
Reducing waiting time and inventory as waste. Furthermore, the goal is to be able to address internal and external influences in such a way that production matches customer demand. The final goal is to reduce production costs.
Steps
- Calculate the Branch time.
- Perform a value add analysis (Yamazumi).
- Identify bottlenecks and steps that do not add value.
- Remove steps that do not add value.
- Identify redundant capacity (time above Branch Time).
- Align capacity to process steps where it is needed as long as the total time of the activity does not exceed the Branch time.
- Check the results and perform the aforementioned steps again where necessary.
Tips:
- See if the process with a long lead time can be done again in parallel. This will ensure a faster turnaround time.
- Provided there is time left over somewhere after the allocation of capacity try to structure it so that this time goes to the last activity. This means a more efficient process and an employee with time left over for other tasks around the process.
- Let people determine the order and combination of tasks and use the computer only for support.
Examples
Activity is above the Branch time:
Figure: Example Line Balancing (current situation)
The excess capacity of Activity 2 is distributed between Activity 1 and 3, making capacity more evenly distributed. This makes the process run more smoothly and does not create surpluses.
Figure: Example Line Balancing (desired situation)
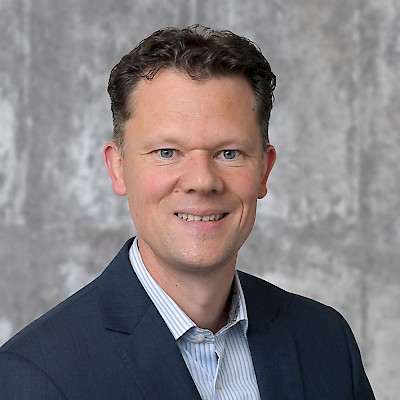